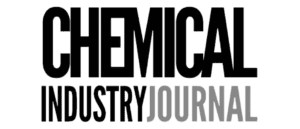
Digital twin technology is reshaping high-risk industries like oil and gas, chemical processing, and energy by enabling smarter, safer, and more efficient operations. However, many still misunderstand digital twins as standalone solutions rather than comprehensive enterprise initiatives that integrate multiple technologies.
In a recent interview with Chemical Industry Journal, our COO, Thomas Grand, shared his expertise on how digital twins, particularly our Shared Reality solution, bridge the gap between static 3D scans and continuously evolving, intelligent models. He highlighted three crucial lessons for successfully deploying digital twin initiatives in industrial environments:
- Transforming 3D reality capture into dynamic 3D models
Traditional CAD-based models fail to reflect real-world site conditions in real time. By leveraging AI and advanced reality capture, companies can transform raw 3D scans into structured, interactive models that adapt as facilities evolve—without the time-consuming “scan-to-BIM” process. - Enhancing HSE risk visibility through virtual models
Safety is a top priority in industries handling hazardous materials. Combining 3D reality models with critical technical data (e.g., Piping & Instrumentation Diagrams) allows teams to simulate safety scenarios, assess risks, and optimize processes like Lockout Tagout before stepping on-site.
- Ensuring data transparency across systems
Outdated documentation and siloed systems create inefficiencies and operational risks. A well-integrated digital twin connects 3D reality models with enterprise asset management (EAM) and maintenance systems (CMMS), improving data accuracy, collaboration, and decision-making across teams.
As digital twin solutions become essential for industrial resilience, companies that embrace a structured, real-time approach will unlock new levels of efficiency, safety, and sustainability.
Read the full article in Chemical Industry Journal